The process of Hot Isostatic Pressing
Hot isostatic pressing (also called HIP or HIPing) is a special manufacturing process that consolidates material and closes pores within parts through the application of heat and pressure. HIP is an established process within Aalberts Surface Technologies in the EU and the US.
depending on your application, there are different process options, with the goal of achieving the desired properties.
HIP uses a furnace inside a pressure vessel and is the simultaneous application of heat and a high pressure inert gas (usually Argon) to materials. The simultaneous application of heat (up to 1250°C) and pressure (up to 207 MPa, 2070 bar) eliminates internal voids and microporosity (no connectivity to the surface) through a combination of plastic deformation, creep, and diffusion bonding. The furnace chamber is heated causing the pressure inside the vessel to increase. Many systems use associated gas pumping to achieve the high pressure level. The gas pressure is applied to the material from all directions (hence the term “isostatic”).
Applying heat and pressure simultaneously eliminates internal voids and defects such as porosity in castings (investment casting) and lack-of-fusion defects in additively manufactured (AM) parts. HIP is effective with almost all materials – including metals, ceramics, and plastic – and can be applied to a large range of alloys including nickel, titanium, steels, aluminum, copper, and magnesium. It improves materials properties such as fatigue resistance, creep, ductility, and workability of parts designed for mission-critical applications. The HIP process densifies, repairs, and creates a uniform microstructure and is the ideal process to improve the reliability and performance of your product by eliminating porosity achieving 100% theoretical density.
As the high pressure atmosphere acts in an isotropic manner on the surfaces of components in the hot zone, the mechanical force exerted is even. This means that solid parts do not see any geometrical change in the HIP. The gas presses on internal cooling channels in the same way as long as they are open to the gas, i. e. with connectivity to the surface. Casting, MIM and AM parts are all possible to HIP, and canned powders can be formed into solid components. In Powder Metallurgy (PM), the HIP process can produce near net shape materials from canned metallic compositions that are difficult or impossible to forge or cast.
HIP is used for the densification and elimination of internal porosity in cast, additive manufactured (AM) and sintered material
Mechanisms: Mechanical deformation / Creep / Diffusion
Isostatic pressure conditions
Inert gas as pressure medium, usually Argon
Same pressure acting on all surfaces in all directions

simultaneous application
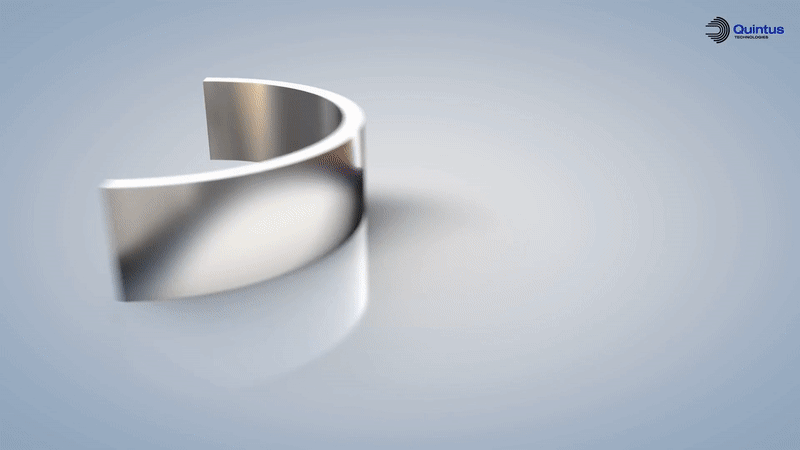
microstructure pre HIP en post HIP
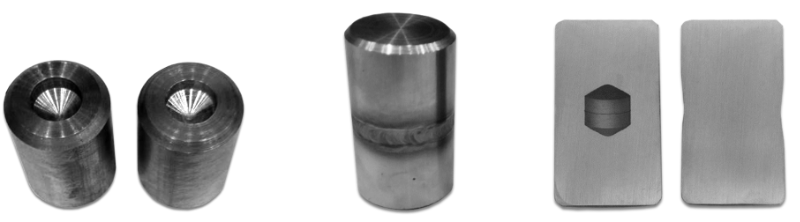
FAQ
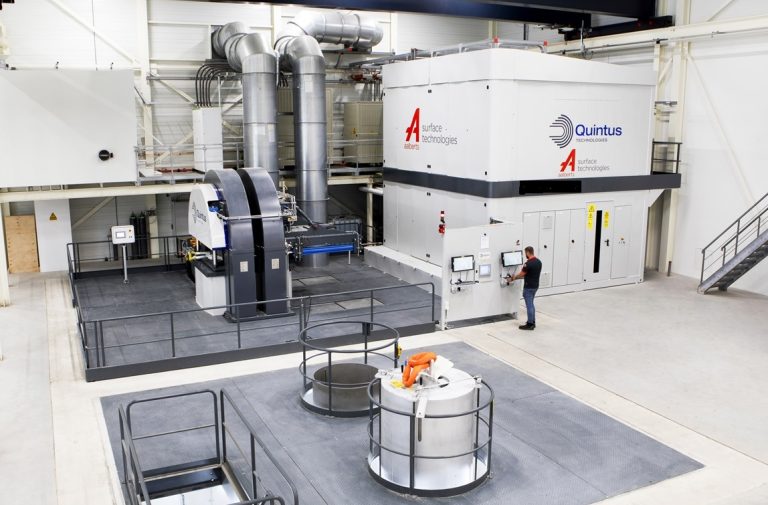